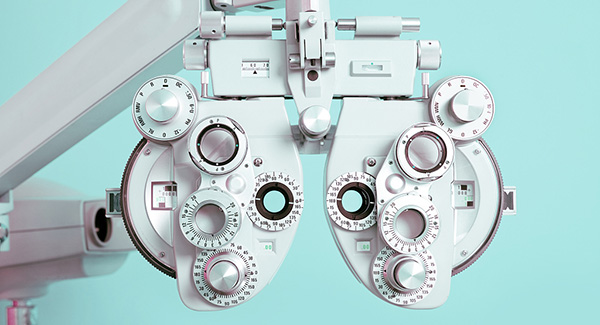
In recent years, the medical device industry has developed rapidly. However, as a typical industry with small size, soft materials and complex shape parts, as a special industry related to quality of life, its product quality testing needs are more stringent and special. Therefore, choosing the most suitable testing equipment will not only enable the medical device industry to obtain product quality assurance, but also help the efficient production and manufacturing, and will also add to the development of new products in the medical device industry.
Composite image measurement technology is the ideal detection tool for the medical device industry. Accurate verification of part size specifications is a key part of small medical device workpiece design and product improvement, especially for medical implant intervention products, minimally invasive interventional vascular stents and The material of the catheter product is soft and the wall is thin and transparent, which makes the contact detection easy to deform. The workpiece characteristics of the nail nail product are too small or even beyond the trigger range of the contact probe. The denture occlusion is not only small in features but also complicated in shape. It is strictly forbidden to detect and scratch any artificial bone joint products whose surface profile is evaluated and whose surface roughness is extremely strict.
Fortunately, imaging and other non-contact detection technologies solve the problems of users in the medical device industry. Non-contact optical detection technology can quickly collect a large amount of three-dimensional information under the premise of the above-mentioned contact measurement disadvantage, which is sufficient for perfect product development. Data analysis and subsequent workpiece size verification; at the same time, the application of CAD-based measurement software enables users to efficiently and intuitively perform dimensional verification, design analysis and manufacturing process control using the 2D.5DD model.
By integrating multiple types of detection technologies such as image, laser, white light and contact in a single device, the most suitable detection method for different geometries, different materials and different reflective properties and accuracy requirements can be obtained: optical image detection means For measuring the planar size and height dimension of thin and soft workpieces, avoiding deformation caused by direct contact; laser measurement is suitable for rapid measurement and mapping of curved surface contours and common geometric features; white light detection technology is suitable for high precision thin and mirror The surface profile and roughness of the material are measured; the normal trigger detection method is suitable for the measurement of all curved surfaces and geometric features that can be directly contacted.
Therefore, sufficient efficiency and flexibility make the composite image measuring system an ideal solution for small, thin, soft and complex types of geometric surveying and mapping in the medical device industry.