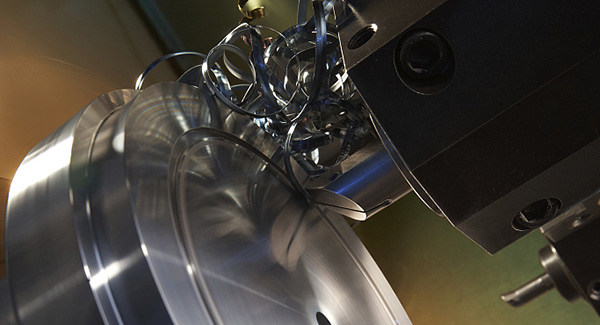
With the continuous innovation of products, the market competition is also intensifying, requiring process equipment companies to provide larger, precise and complex molds and tooling products, while requiring more economical and faster delivery times. In this case, the mold manufacturing technology needs to be continuously improved to meet the requirements of informationization, digitization, refinement, automation and on-site, and the flexible and agile manufacturing is completed by rapid prototyping technology and reverse engineering technology. And the digital flow forms a closed loop of enterprise manufacturing information.
Stamping die inspection program - large-scale measurement technology on site
The stamping die represented by the automobile cover mould has set strict requirements on the measurement technology in the fields of processing, production, trial production, trial production and parts. This includes the preparation of casting blanks, processing and testing of complex profiles, mold trials and mold clamping analysis. In view of the large size and complex shape of stamping dies, more on-site measuring systems are required to penetrate, process, manufacture and assemble. The whole process of test mold clamping and even part measurement and copy repair.
01 casting processing link
The processing of stamping die blank castings is currently popular for lost foam processing, that is, using soft materials such as sludge, resin, and plastic foam to form a lost foam mold. The traditional lost foam machining method is an engraving machine or a heavy-duty CNC machining machine. These machining solutions have limitations in processing size, need to fix the foundation, and have large investment. The ROMOCUT flexible robot milling system overcomes the above-mentioned drawbacks: it can be moved, does not require foundation and machine room, can realize multi-position movement processing to achieve unlimited expansion of high-precision machining range, and can also be equipped with hollow milling cutter and vacuum chip removal for plastic foam material. The system ensures a clean and pollution-free processing environment. ROMOCUT is a new generation replacement for traditional lost foam milling systems.
02 on-site measurement link
In the stamping die processing stage, the most efficient measurement solution is the first to push the portable field measurement solution —— the joint arm that can be measured at startup, flexible and suitable for hidden point measurement, and the surface point cloud with high efficiency and large area The superior photo-measurement system and the laser tracker that wins with high-precision and large-size measurement range, of course, also include on-machine measurement solutions that can feed back the machining results in real time in the process. The advantage of on-site measurement solutions is the ability to provide timely reference data for high-efficiency visualization of molds.
03 test mode
Through the analysis of the mold clamping of the concave and convex mold and the analysis of the shape and springback of the prototype, the mold is adjusted and modified, and finally the correct shape of the workpiece is obtained. The large-scale curved shape is a remarkable feature of the stamping die and its parts. Therefore, the comparison between the die-type point cloud and its CAD is the most efficient data analysis method. The CognitensWLS400 camera-based measurement system enables high-speed acquisition of single large-area, high-precision point clouds in demanding industrial environments that are immune to vibration and illumination, and data processing such as virtual assembly and batch data statistical analysis for point clouds. CognitensWLS400 can complete the inspection tasks of various parts of the mold, tooling and its parts, and can be used for the whole process quality control of the mold from processing to delivery.
04 Precision Measurement
The mold frame of the stamping die is a component that transmits pressure and ensures the positional accuracy of the die. The positional precision of the upper guide post, the guide bush and the guide pin are required to be high. The universal precision measuring equipment is a fixed (bridge, gantry, cantilever) measuring machine that can perform high-precision quality verification. The DEA gantry measuring machine adopts an open structure and a foundation-type platform, which is not limited by load bearing, and is convenient for the large stamping die to be placed and loaded.
05 equipment adjustment
When stamping a part with a stamping die, it is usually necessary to perform precision correction on the processing equipment. The Leica Absolute Tracker is the ideal solution for aligning, installing and calibrating large equipment. With the unique PowerLock automatic target locking function, the Leica Absolute Tracker is capable of precision alignment and inspection up to 160m in a complex workshop environment with a reflective ball.
06 Parts inspection
Verification of the position and shape of the stamping part will determine whether the mold can be delivered, and the rapid and repeatable data acquisition and evaluation of the stamped surface is the key to complete the measurement and analysis of the part. The fixed measuring system (bridge, gantry, cantilever measuring machine) equipped with the new CMS series laser scanner enables automatic and efficient inspection of stamped parts surfaces. CMS has good adaptability such as automatic exposure, can adapt to various materials of different materials and colors, different brightness, variable line width, variable point distance intelligent features, making the workpiece surface point cloud more efficient. The high-paced on-site quality control of the mature parts production line can be automated with the CognitensWLS400A robotic camera.
07 inspection tool
The inspection tool is the inspection standard for large-volume parts on the production line. According to the different precision requirements of the inspection tool, fixed measuring equipment or portable field measuring equipment can be selected.
08 copy and repair
Successfully delivered molds need to be archived, and finished molds in use need to be quality controlled at any time to repair wear or copy. The Cognitens photogrammetric system and the ROMER absolute articulated arm with high-efficiency laser scanning probes enable efficient acquisition of mold point cloud data, CAD data comparison analysis, or assisted reverse modeling.